News & Updates
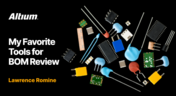
Check out our article, where Lawrence Romine shares his top tools for conducting efficient Bill of Materials (BOM) reviews in PCB design. It highlights key features in Altium 365, Octopart, and ActiveBOM that help engineers avoid unsourceable components and streamline procurement.
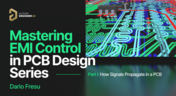
As the first article in the "Mastering EMI Control in PCB Design" series from our new asset Dario Fresu, this piece explores signal propagation in PCBs, highlighting the crucial roles of impedance, dielectric materials, and trace geometry in maintaining signal integrity.
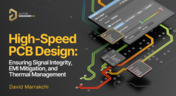
Discover essential strategies for high-speed PCB design, focusing on signal integrity, EMI mitigation, and thermal management. Our latest article provides insights on managing crosstalk, optimizing grounding, and addressing thermal challenges to ensure reliable PCB performance.
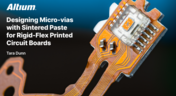
Designing microvias with sintered paste in rigid-flex PCBs offers enhanced electrical conductivity and mechanical strength, crucial for high-density applications. Our new article explores the benefits of sintered paste and provides essential design tips to optimize microvia performance and reliability.
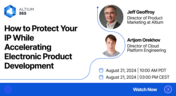
Watch our webinar to learn how our centralized electronics design data platform can quickly integrate with your IT access, tracking, and compliance tools, while also making it easier to work in teams.
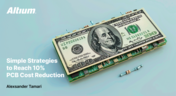
Our new article outlines strategies to achieve a 10% reduction in PCB costs by optimizing design and material choices, such as adjusting stack-up materials and hole sizes, using lower-cost parts, and considering single-sided assembly. These techniques help reduce expenses without sacrificing quality.
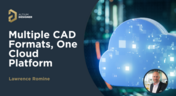
Check how Altium 365 helps eliminate EDA software vendor lock by enabling multi-CAD support in the cloud. This allows users to work with different CAD file formats within a single platform, enhancing collaboration and reducing the need for additional licenses. This approach offers greater flexibility and is set to transform the industry.
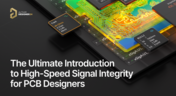
High-speed signal integrity is essential in PCB design to ensure data accuracy and system reliability. Key issues like impedance mismatches, crosstalk, and signal reflections need to be addressed through strategies such as controlled impedance traces, differential pairs, and suitable material choices. Check out our first article of the series about this topic.
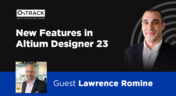
Altium’s VP of marketing Lawrence Romine discusses the multi-board and harness design capabilities coming in Altium Designer 23.

Controlled ESR capacitors are important for power integrity in your design as they can help smooth out the PDN impedance spectrum in your high speed PCB.
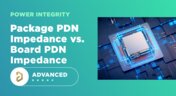
Whenever we say something to the effect of “components can’t work without a correctly designed PCB,” we only have to look at component packaging for evidence. It is true that component packages come with parasitics that affect signal integrity, but there is one area that we don’t often look at in terms of component packaging: power integrity.
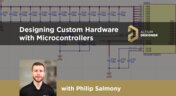
In this article, we’ll look at all that is required to start creating your own custom microcontroller-based hardware designs. You’ll see that there actually isn’t too much to this, as microcontroller manufacturers over the years have tried to make the learning curve less steep and their devices more, and more accessible. This is both from an electrical point of view but also – equally importantly – from a programming point of view.
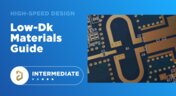
If you’ve taken time to learn about PCB material options and layer constructions, you have probably seen the wide range of materials that are available on the market. Materials companies produce laminates with varying Dk values, Tg values, weave styles, CTI values, and mechanical properties to target various applications in the electronics industry.
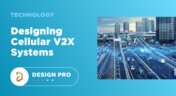
If you’re waiting for truly connected cars on a grand scale, there is still a massive amount of work to be done, both on the hardware and software sides. Connected cars can only become a widespread reality once the automotive industry and telecom carriers can decide which protocol will work best for vehicle-to-everything (V2X) communication. PCB designers will then need to step in to create these systems and fit them into a vehicular environment.
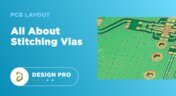
This one area of PCB design can be contentious among some designers as it is related to copper pour, which it is often stated is not needed in most designs. Regardless of your feelings about copper pour, stitching vias have important uses in PCBs at low frequencies and at high frequencies.
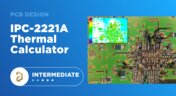
The IPC-2221 standard includes many requirements for printed circuit board design and manufacturability, and there are several online calculators that have been developed based on this standard.
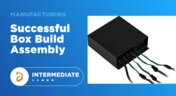
When you’re ready to manufacture a new device at production volume, there are many aspects of the product that must come together. The enclosure, cabling and connectors, embedded software/firmware, and of course the PCBA all have to be considered in totality. There is a quick way to get your product into a usable enclosure, complete with input power and cabling, and with a form factor that fits your PCBA. This overused route to a new product is a box build assembly.
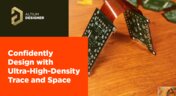
Printed circuit board fabricators have become skilled at manufacturing these technologies and also at understanding the reliability and producibility challenges associated with high-density-interconnect technology. Let’s look at where the PCB industry is at today.
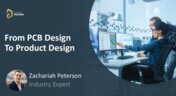
What can the industry do to support PCB designers as they continue taking a more active role in product development? Here at Altium, there has been a progressive shift towards looking at the system level and creating tools that get designers more involved throughout the product development process. As the saying goes, over the wall engineering is over… today’s most successful products are built in a collaborative process.
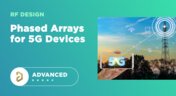
As the 5G rollout progresses and researchers continue to discuss 6G, many new 5G-capable products operating in sub-GHz and mmWave bands are reaching the marketplace. Devices that will include a 5G-compatible front-end, whether small stations/repeaters or handheld devices, use phased arrays as high-gain antenna systems to provide high data throughput without losing range at higher frequencies.
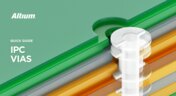
Via protection is an important part of modern PCB design. It provides additional benefits in PCB manufacturing and assembly, increasing the number of acceptable products.
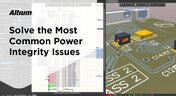
Power integrity problems can abound in modern PCBs, especially high-speed boards that run with fast edge rates. These systems require precise design of the PDN impedance to ensure stable power is always delivered throughout the system.
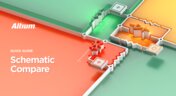
A design project doesn’t appear out of nowhere. The design process spreads over time, and project documents change. Schematic documents gradually become more complex, new functional blocks appear, and already finished parts can be modified and updated.
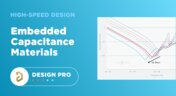
Capacitance is your friend whenever you need stable power integrity, which is why there is so much focus on decoupling capacitors. While these components are important and they can be used to provide targeted power integrity solutions to certain components, there is one specialty material used to supercharge capacitance in your PCB stackup or package substrate.

Getting started with design rules can sometimes be a difficult task, but it doesn’t have to be. Altium Designer has added a new design rules user interface along with a new way to define rules, while not compromising past methods. Now, rules and constraints have a design-centric view rather than a rules-centric view which allows for easier visualization and is less prone to error. Watch this video to learn how you can best utilize the improved Rules 2.0 design rule interface.

Working between the Electronic and Mechanical design domains brings unique challenges. ECAD and MCAD tools have different design objectives and have evolved down different paths, and so has the way they store and manage their design and project data. Watch this video to learn about seamless ECAD/MCAD Collaboration on the project, how to comments for other design teams and how to review, Approve or Reject design changes from your mechanical engineer.
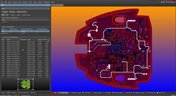
Do you ever have to edit a large group of objects on your design? Whether you are dealing with your schematic or PCB, this webinar will help you get acquainted with the main tools for group editing of objects in Altium Designer. You will also learn how to effectively apply group editing methods with filters and selection tools in different design scopes.

Version control has been a staple of software development for decades, but hardware development can benefit just as much from a version control system (VCS). Traditionally, VCS has been managed locally tying you down to a workplace, but advances in cloud technology have removed that limitation. Learn how Altium 365 cloud technology enables working concurrently on designs with built-in version control and evaluate its advantages.
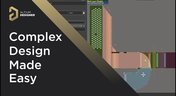
The design process often requires repetitive work with tedious tasks. Altium Designer 21 represents a better way to design by revitalizing long-standing functionality and improving the user experience, as well as performance and stability, based on the feedback from our users. These improvements streamline existing design tasks and empower you to complete sophisticated rigid and rigid-flex designs with realistic 3D modeling.

Printed Electronics is emerging to become as common as 3D printing. With this fast-emerging technology, new possibilities have come into the manufacturing arena, allowing engineers and designers to develop products in markets never before realized. With the emergence of many contract manufacturers possessing this capability, the cost is competitive. Quick-turn prototypes and volume production are now all possibilities, and with Altium 365® you stay connected directly with your manufacturer throughout the design process.
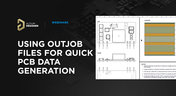
An OutJob is simply a pre-configured set of outputs. Each output is configured with its own settings and its own output format, for example, output to a file or to a printer. OutJobs are very flexible – they can include as many or as few outputs as required and any number of OutJobs can be included in a project. The best approach is to use one OutJob to configure all outputs required for each specific type of output being generated from the project.
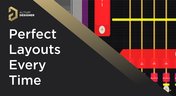
Getting your PCB layout design done takes patience and precision. Complex footprint geometries, board shape, and dense component placement require accurate primitive positioning. Each stage of PCB design needs a different snapping configuration. Often your settings can be excellent for one stage and be unfavorable for another. Learn more about different snapping usage patterns and best practices of efficient snappings.
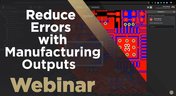
No one wants to do a board respin because of inaccurate or incomplete manufacturing outputs confusing design intent. This webinar covers the information needed for PCB Manufacturing and Assembly, as well as, a simple way to communicate and collaborate with manufacturing.
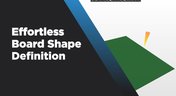
You need to define your PCB geometry in the context of your enclosure. If your board cannot physically be assembled into the final product, it doesn't matter how well laid out it is electrically. This webinar focuses on how the MCAD CoDesigner allows you to edit your PCB in the context of a higher-level assembly, allowing you to respect the relevant mechanical constraints.
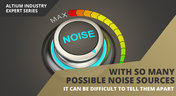
You need to define your PCB geometry in the context of your enclosure. If your board cannot physically be assembled into the final product, it doesn't matter how well laid out it is electrically.
This webinar focuses on how the MCAD CoDesigner allows you to edit your PCB in the context of a higher-level assembly, allowing you to respect the relevant mechanical constraints.